Tire recycling: How McMaster University chemists use silicone chemistry to dissolve used tires
- macmuscs
- Oct 13, 2021
- 3 min read
Updated: Oct 16, 2021
A research group at McMaster University has found an innovative process for the break down of rubber in used automotive tires. This process has the potential to lead to new recycling methods for a process that was once thought too difficult to achieve.
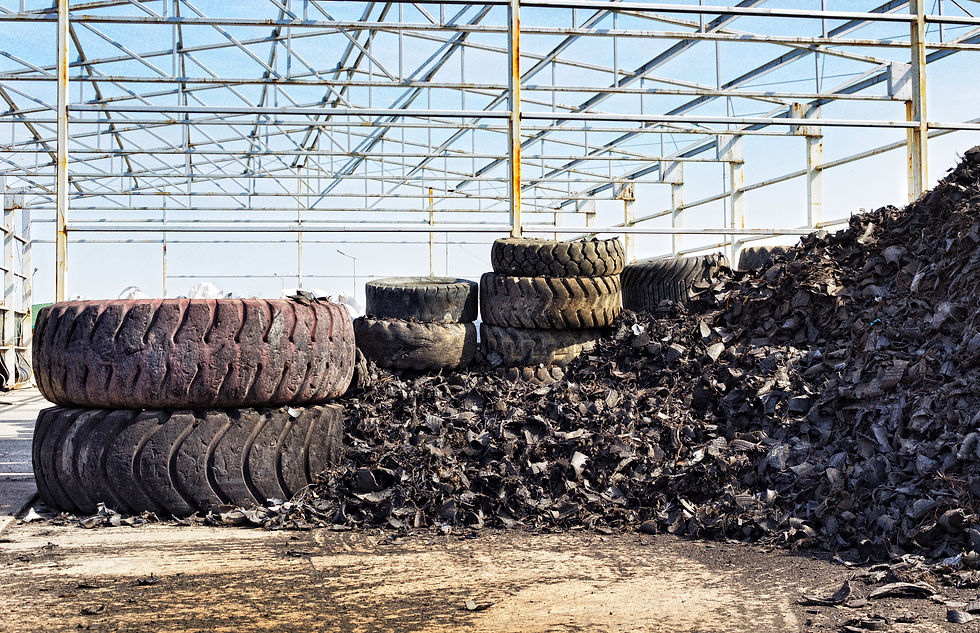
Charles Goodyear, a household name for many and the name behind Goodyear tires, is the father of rubber vulcanization and subsequently tire production. In 1844, Goodyear reported the accidental dropping of natural rubber mixed with sulfur on a hot stove, resulting in properties like improved elasticity, resilience, tensile strength, weather resistance and hardness.(1) This is a result of a process known as vulcanization, which involves the radically induced bridging of natural poly(isoprene) polymers with sulfur at elevated temperatures.(2) This allows for the formation of cross-linked poly(isoprene), which transforms the polymer from a fluid state to the product we know as tires (Figure 1).

Figure 1. Mechanism of vulcanization of natural poly(isoprene) rubber with sulfur.
This complex cross-linked network may allow for many fantastic properties, but also lends hand to difficulties in processing and breakdown of rubber-based products like tires.(3) Resultingly, tires pose a significant environmental burden and end up in landfills, leading to leaching of dangerous contaminants into surrounding land.
In fact, a 14 million tire pile-up in Hagersville, Ontario is a local example of the environmental and human risks these products pose.(4) In 1990, this pile-up resulted in a 17 day long out-of-control burning that released toxic smoke and breakdown products into the neighbouring areas. Thousands of residents had to evacuate their homes, and the released toxins have been connected to long-term health complications like cancer.
In a world moving toward more sustainable processes, chemists are constantly working toward the ability to remove single use products or assist in successful and environmentally friendly breakdown. Tires are a prime example of a mostly single-use product that is made from non-renewable resources. In some instances, tires can be reused for fuel in the cement industry or even as fillers in asphalt and artificial turf.(5) However, until now there hasn’t been an efficient process for the recycling and recovery of the petroleum-based polymer building blocks for reuse or repurposing.
This is until recently, as a group of researchers at McMaster University led by Dr. Michael Brook discovered a process to break down old tires, publishing an article titled “Dissolving used rubber tires” in the journal of Green Chemistry. This method focuses on the efficient degradation of the horizontal sulfur cross-links in the organic elastomers, breaking apart the highly cross-linked polymer matrix back into its constituent polymer “ropes”.(6) The process first begins with cutting the tires and shredding them into a crumb-like granulated consistency. These rubber granules are then treated with a variety of hydrosilicones and 10 wt% of a Lewis acid Tris(pentafluorophenyl)borane (BCF) catalyst for upwards of 45 minutes. These two in concert allow for a process known as reductive sililyation of the RS-SR bonds into silyl thio ethers (RSSiR”3).
In temperature ranges from room temperature all the way up to 100 °C, the group was able to recover anywhere from 56% yield for complex rubber mixtures, all the way up to 93% yield for butyl rubber. A simple filtration step follows to remove inorganic materials like carbon, metals, silica, and polyester cord fibers. The recovered polymeric oils are very similar to the original polymers used in production. Thus, they can then be collected and reused by radically or oxidatively crosslinking them to generate new elastomeric products, which can be reinforced with the previously extracted inorganic solids (Figure 2).
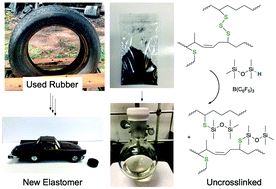
Figure 2. Breakdown of used rubber with BCF and hydrosilicones. The resultant uncrosslinked polymers can be repurposed for the production of new elastomers. Figure from reference 6.
Although this process has seen significant improvements to a once thought impossible challenge, the group suspects limitations of the treatment technique when used at an industrial scale. For the efficient reduction of rubber at scale, large quantities of the BCF catalyst will be required. This imposes significant cost implications and will require further work to increase efficiency of the breakdown step with less material. This process is not quite ready for commercial use, but serves an important steppingstone to solve an increasingly dangerous environmental issue posed by automotive rubber.
The findings of this research has been published in the Journal of Green Chemistry:
Zheng, S.; Liao, M.; Chen, Y.; Brook, M. A. Dissolving Used Rubber Tires. Green Chem. 2020, 22 (1), 94–102. https://doi.org/10.1039/C9GC03545A.
References
1) C. Goodyear US Patent , 3633, 1844.
2) A. Y. Coran The Science and Technology of Rubber (Fourth Edition) , J. E. Mark, B. Erman and C. M. Roland, Academic Press, Boston, 2013, 337–381.
3) Freedonia Group, 2015, Industry Study 3357.
4) https://brighterworld.mcmaster.ca/articles/mcmaster-chemists-find-new-way-to-break-down-old-tires-into-material-for-new-ones/
5) Rubber Recycling: Challenges and Developments , J. K. Kim, P. Saha, S. Thomas, J. T. Haponiuk and M. K. Aswathi, RSC, 2019.
6) Zheng, S.; Liao, M.; Chen, Y.; Brook, M. A. Dissolving Used Rubber Tires. Green Chem. 2020, 22 (1), 94–102.
Comments